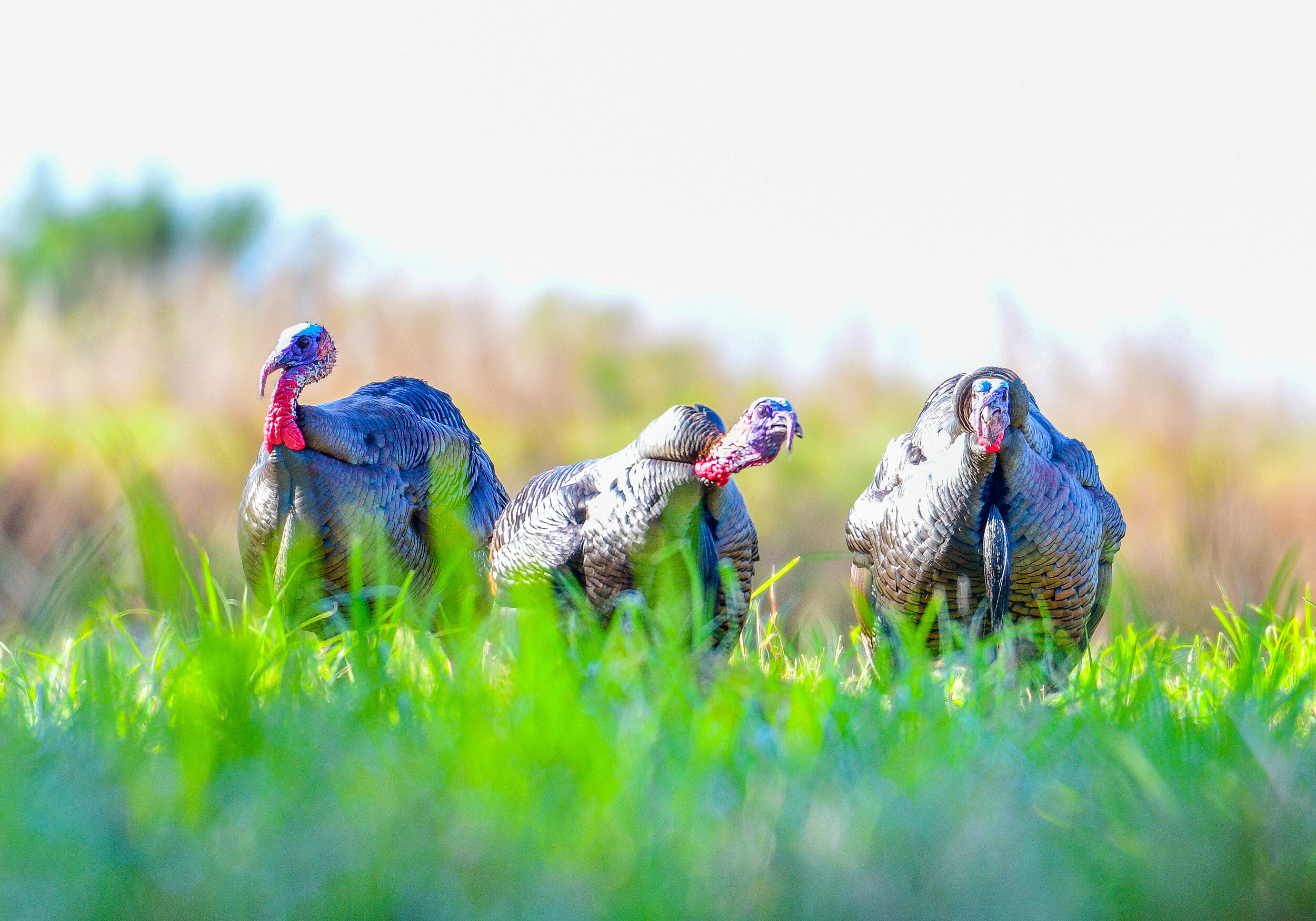
The Process of Making a Custom Turkey Trumpet Call
“Absolute precision process needed for consistent sound and repeatability. The recipe tolerances must be kept as close to +/- .001” as possible for desired results to be obtained.”
First, high quality wood blanks are purchased. Wood blanks are then dried to appropriate moisture content in a humidity controlled storage room. Next each blank is sized to the proper dimensions. Then, I find the centers on the wood blanks and secure them on a wood lathe. After that, I drill the blanks with multiple bits, specialized reamers, and bell cutout treatment. Next I sand the barrel to the final specs. At least 20 coats of very thin CA finish are applied to the wood barrel exterior, as well as 2 coats on the interior. I then wet sand from 1000 grit through 12,000 grit and finish with a special polish to a high sheen. The mouthpiece material is next, I drill each one specifically to match the recipe, much more than meets the eye here. The mouthpiece is shaped, sanded, polished, and tuned to the body before final gluing. Part of the final tuning is adjusting the overall length of mouthpiece, this will affect tone and playability of the trumpet. The mouthpiece is just as important as the barrel for overall sound, tone, & playability.
The brass ferrule is custom turned to create a seamless union between the mouthpiece and wood barrel. The wood barrel, mouthpiece, and ferrule are glued together. Lastly, a EVA or wood lipstop is turned to fit the specific mouthpiece. Then a turkey trumpet call is born!
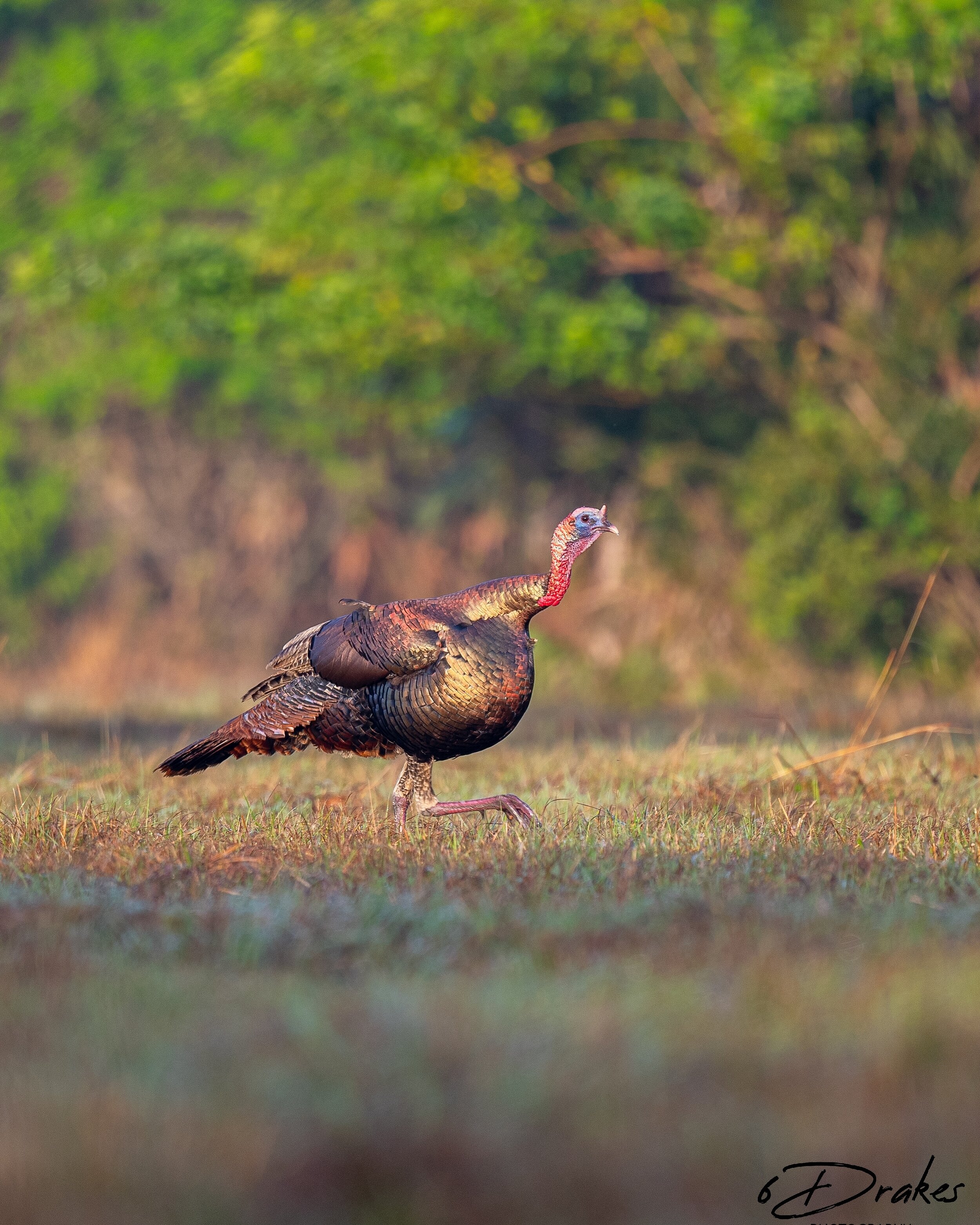